CAN bus analysis of electric vehicles vs. combustion engines
A Geotab solutions engineer explains CAN bus analysis in vehicles and how connecting to EVs works.
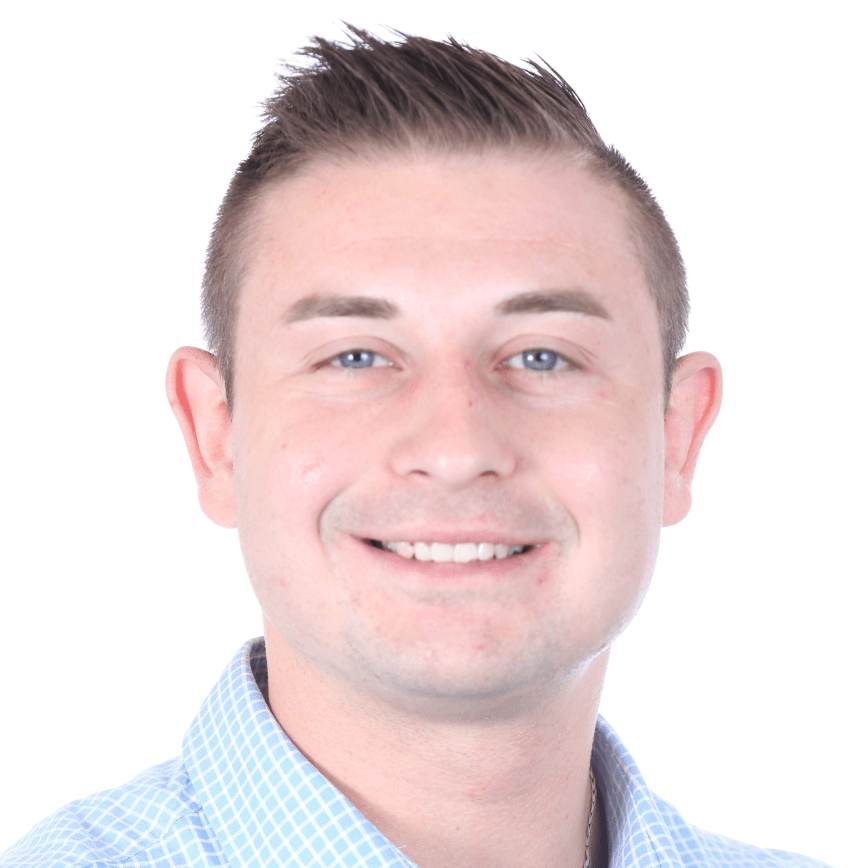
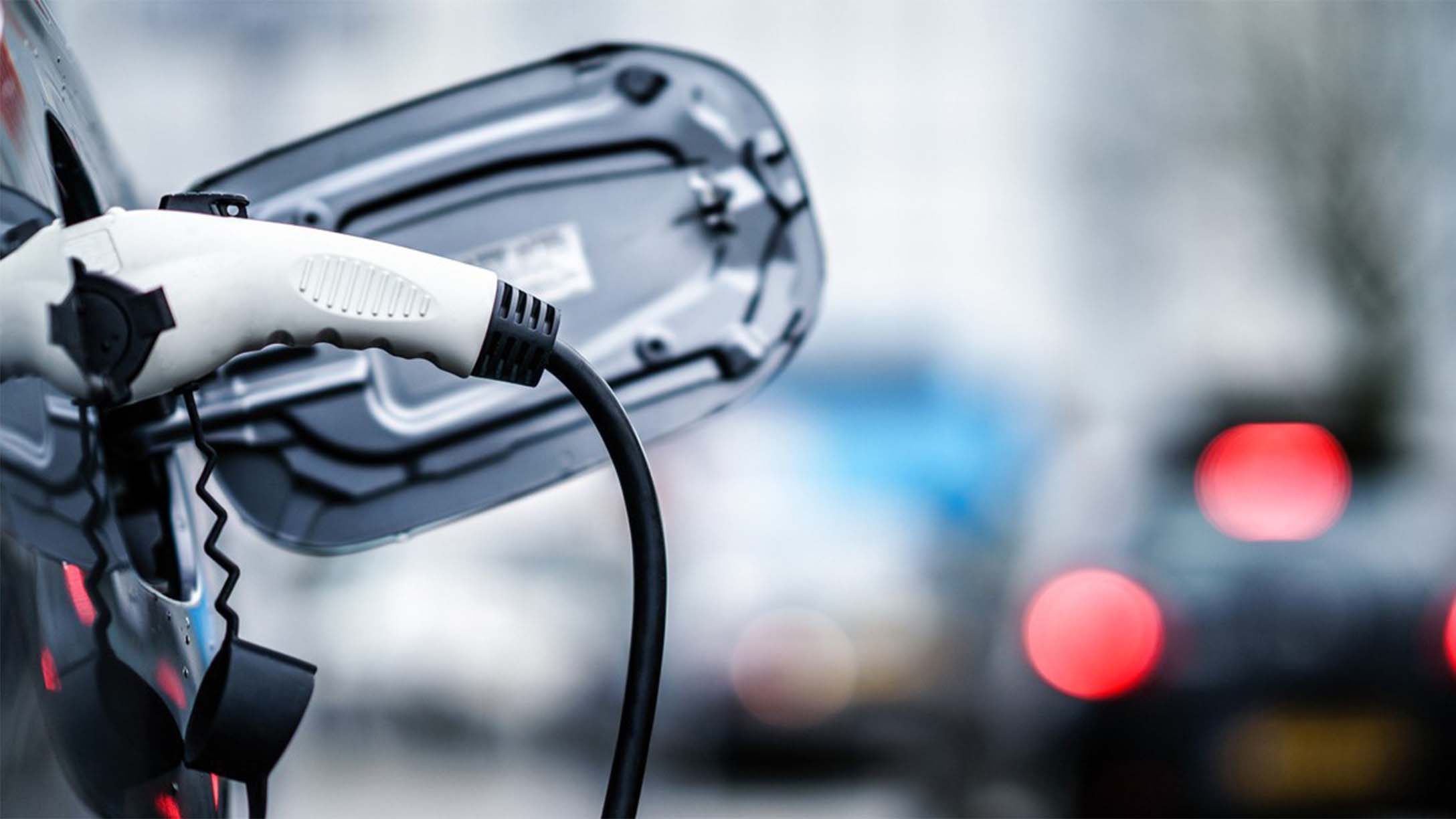
As electric vehicle adoption rises around the world, the challenge of integrating those vehicles into a fleet management program emerges. Achieving company goals like safe driving or reducing emissions requires all drivers and vehicles to work together. However, fleet tracking electric vehicles (EVs) is possible. This article takes you behind the scenes, to explain how connecting to EVs works.
Plugging in to EV intelligence
Fleets can connect to traditional gas-powered trucks, vans or cars by installing a small, GPS tracking device. In the case of EVs, there is no difference — the process is totally similar.
The next step is to send the EV data to MyGeotab so the fleet manager can view and manage operations remotely. To make that happen requires skilled engineering.
Quick intro to reverse engineering
You may have heard that it is harder to reverse engineer an EV than a vehicle with an internal combustion engine. First, let me clarify quickly what the term “reverse engineering” means, as you can reverse engineer a lot. For this post, I am referring to reverse engineering in terms of the CAN bus system in vehicles. At this point you may ask yourself: Well, what exactly is a CAN bus? Good question!
The CAN bus system (controller area network) connects all engine computer units (ECU) in modern vehicles today, which facilitates communication between all ECUs. This might sound easy in theory. However, it is one thing to connect all ECUs, but a whole different story to send messages with them.
ECUs use different types of protocols to send messages. These protocols may be compared to different languages. What do I mean by that? Not all ECUs use the same protocol (or language), which is why there are not able to understand each other. This is why you have to find the right language to “talk” to them.
See also:
All in all, the quantity of rich engine data you can receive from an CAN bus system, heavily depends on its construction.
By the way, did you know that a vehicle today provides more than 70 ECUs? This indicates that newer vehicles provide a larger amount of data than older vehicles.
Where does reverse engineering an EV differ from reverse engineering a combustion engine?
The first important differentiator is that in EVs, there is no list of standardized data, which is typically found in combustion engines. By list of standardized data, I refer to the OBD II standard format, which is where the data points relevant to fleet tracking are located.
In the EV context, the information is located in different locations, which depend on the manufacturer and are therefore unique. The second differentiator is based on the history of the OBD II port. The OBD II port was originally created in order to support garages in providing service for vehicles with regard to the emissions of vehicles. Logically, an EV does not produce any emissions while driving. Following, this underlines the key point: The CAN bus from an EV is constructed differently than the CAN bus from a combustion engine.
All in all, we have established why reverse engineering EVs differs significantly from reverse engineering combustion engined. Nevertheless, Geotab has the capability to manage the different hurdles regarding EV tracking in an efficient and productive way. The Geotab GO9 fleet tracking device supports fleet management of EVs through MyGeotab.
Learn more about the benefits of fleet tracking electric vehicles on our EV page.
More from EV news:
Subscribe to get industry tips and insights
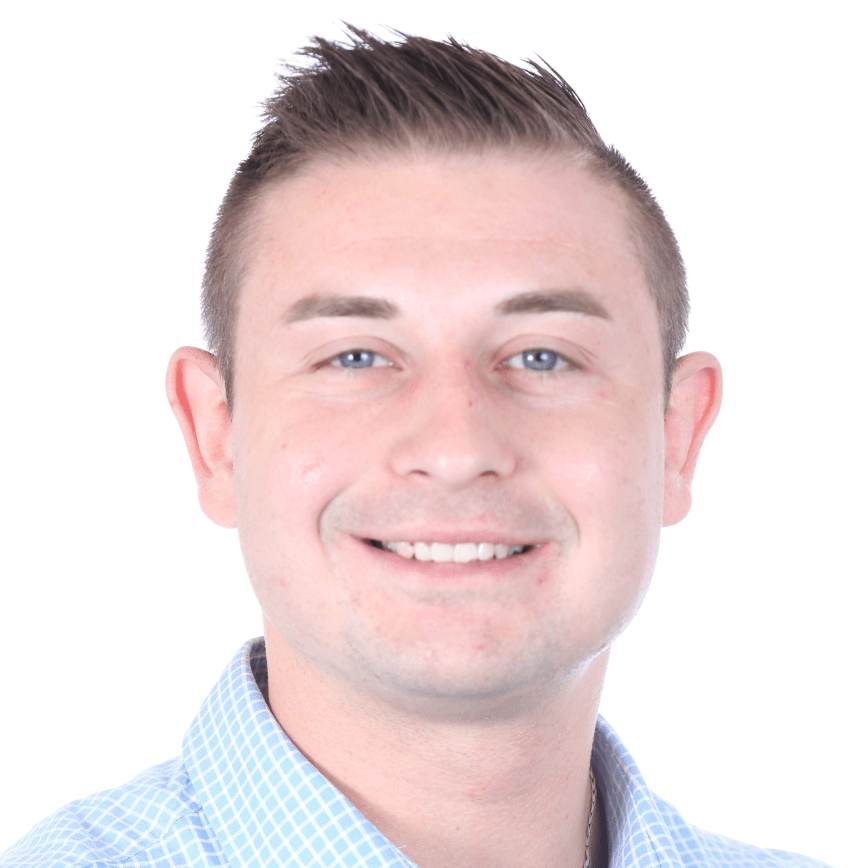
Markus Gajda is a Solutions Engineer for Geotab.
Table of Contents
Subscribe to get industry tips and insights
Related posts

What is government fleet management software and how is it used?
April 10, 2025
3 minute read
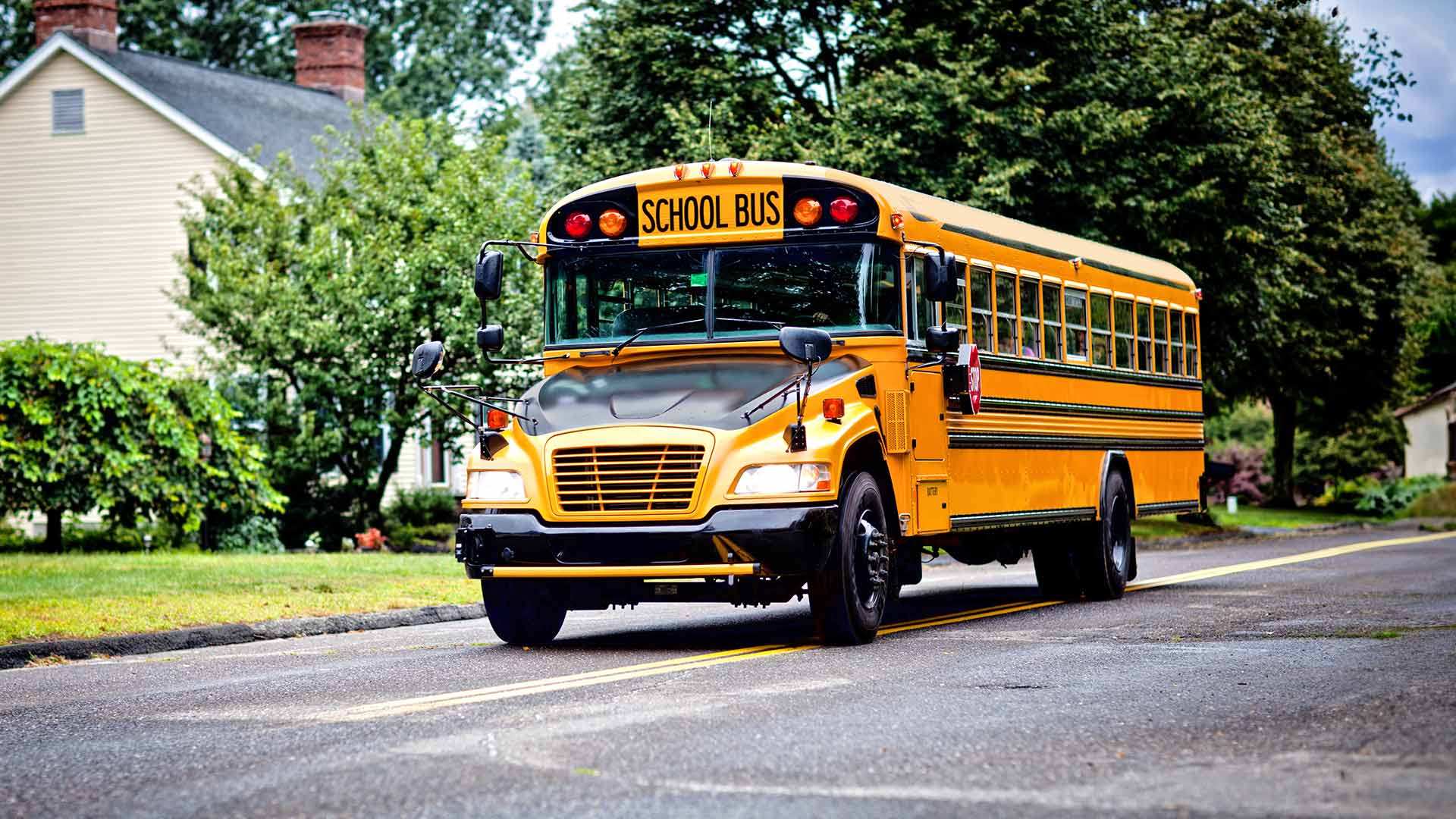
Enhancing student bus safety: Combating distracted driving in the digital age
April 7, 2025
6 minute read
.jpg)
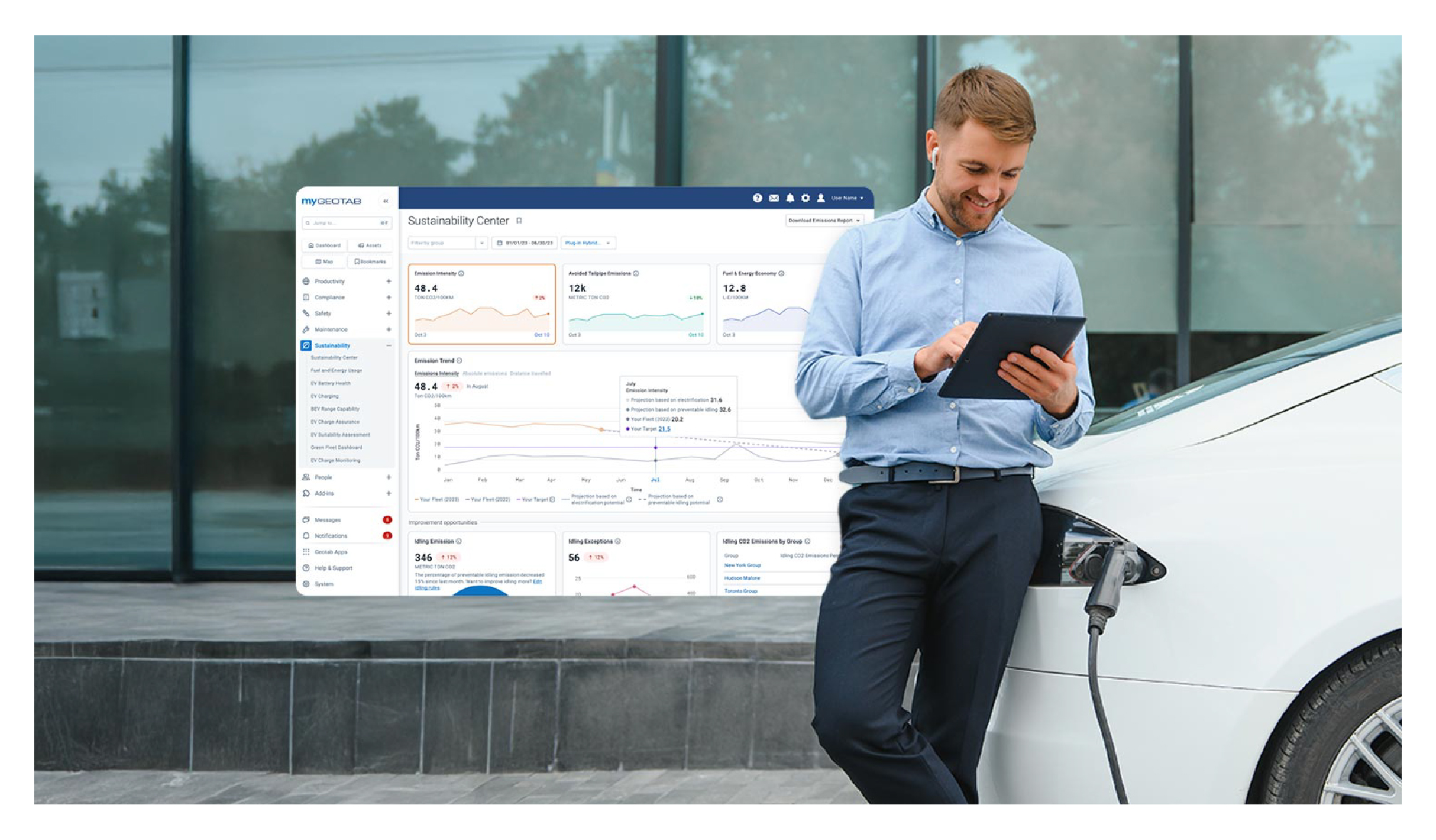
Geotab’s new fleet Sustainability Center simplifies fuel and emissions reduction
March 3, 2025
3 minute read
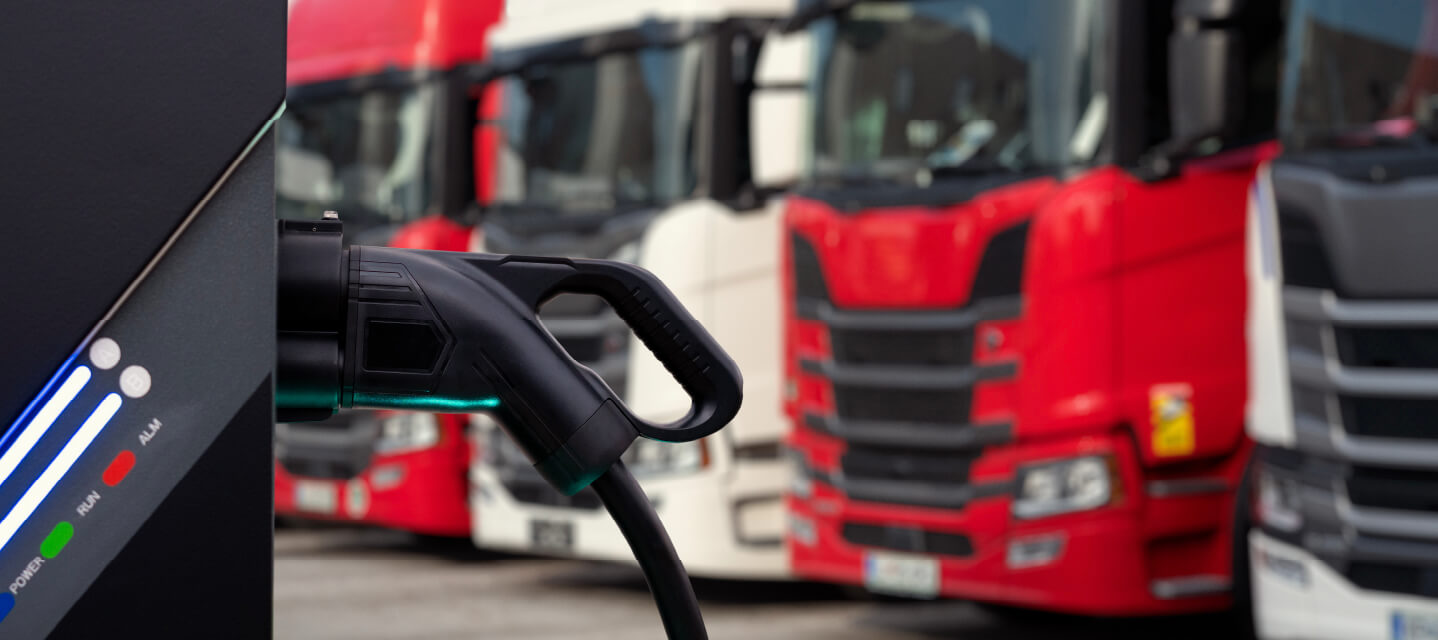
How long do electric car batteries last? What analyzing 10,000 EVs tells us…
January 20, 2025
9 minute read