How to avoid high downtime costs for construction fleets
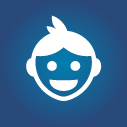
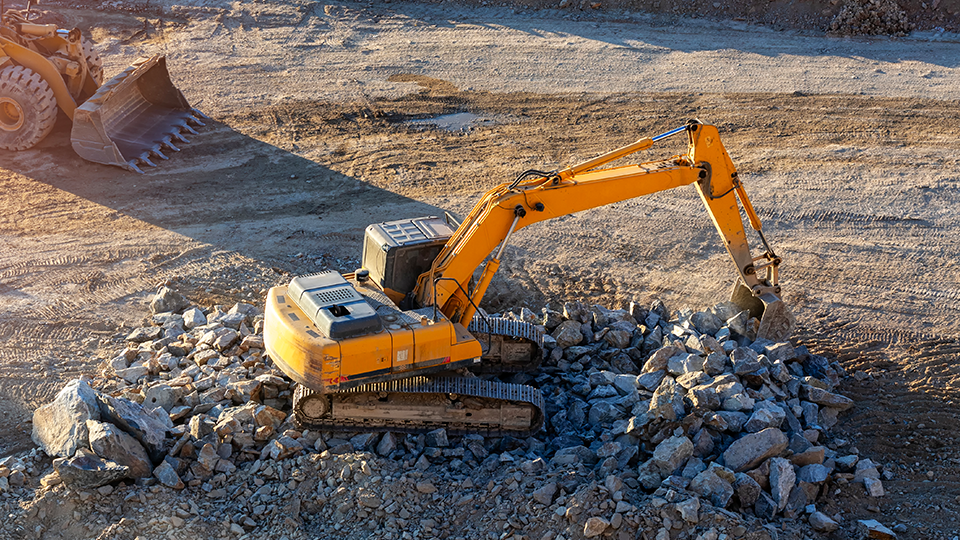
Key Insights
- Downtime is a major drain: Learn why only 8.5% of construction projects finish on time and on budget, and how to combat costly equipment downtime.
- Data-driven solutions: Discover how telematics and data analysis can optimize maintenance, prevent theft, and streamline operations.
- Actionable steps to uptime: Get a free checklist to implement proactive maintenance, improve equipment utilization, and enhance workflow efficiency.
Downtime. It’s a big reason only 8.5% of construction projects are completed on time and on budget. Every hour of equipment downtime means lost revenue, missed deadlines and frustrated stakeholders. How can you stop unexpected mechanical failure, inefficient workflows or even stolen assets from causing downtime that derails your construction projects?
The answer lies in embracing data-driven strategies. Data is the key to understanding where you are losing out on time and money, giving you more visibility into how to streamline your operations. We know your next question – how do you get this data? And more importantly, how do you use it to inform your fleet decisions?
In the next couple of paragraphs, we’ll delve into some of the most common culprits behind construction equipment downtime, exploring how telematics solutions offer a powerful arsenal of tools to combat these issues. We'll examine specific examples of how telematics can help optimize maintenance schedules, improve equipment utilization, prevent theft and ultimately contribute to a more efficient and profitable operation.
The four major causes of construction fleet downtime
Downtime doesn’t just happen out of nowhere. By recognizing the four primary causes of downtime, construction managers can start creating a data-driven strategy to address them and drive operational efficiency across their projects.
Reactive maintenance:
You know every construction asset will eventually require maintenance — but if you wait until an asset has obvious performance issues before servicing it, you’re more likely to face more expensive repairs. This wait-and-see approach is known as reactive maintenance, and it plays a huge part in increasing downtime for construction projects. Instead of waiting for breakdowns, use telematics data to monitor equipment health and schedule maintenance before issues arise. This enables proactive maintenance of your equipment that helps prevent costly spontaneous repairs and unexpected project delays.
Equipment misplacement and theft:
Juggling a large construction fleet spread across multiple work sites is like trying to herd cats – except these cats weigh several tons and cost a small fortune. We all know that keeping tabs on all of your powered and non-powered assets is a time-consuming and laborious task. However, not knowing the whereabouts of your equipment increases the risk of downtime from improper usage, mistakes in deployment and even theft. To better manage all your assets, adopt a telematics solution with GPS tracking to give your fleet managers real-time insight visualization of where all your assets are, whether they’re onsite or in transit. This prevents downtime by improving security and minimizing delays from deploying assets to the wrong locations.
Inefficient operations:
The sheer number of daily decisions that a construction manager has to make, each impacting a vast array of machinery, can quickly become overwhelming – and let's face it, complexity breeds downtime. The more moving parts you have, the more opportunities there are for things to go wrong. But what if you could cut through the chaos and gain a clearer picture of your entire operation? The key lies in data. The more data you can draw across your construction operation, the more you can optimize operations. By analyzing usage patterns, managers can deploy assets more efficiently while preventing unnecessary idling and underutilization. Reports on fuel consumption, idle time and equipment hours also help improve decision-making to keep projects on schedule.
Convoluted workflows:
Construction projects involve more than just equipment. If you have rich data about your fleet operations but lack insight about your materials, employees or customers, you are going to face downtime. This is why it’s important to integrate telematics data with other business systems to enhance efficiency across your operations. By consolidating maintenance schedules, equipment tracking and utilization reports in a centralized platform with other operational data, construction managers can seamlessly share insights between teams to streamline workflows and boost uptime.
Solution: The construction manager’s guide to maximum uptime
Want to take control of your equipment uptime and minimize costly delays? We’ve created a comprehensive checklist to help you do just that. By downloading our free checklist, you will take actionable steps towards:
- Enabling proactive maintenance
- Tracking equipment and prevent theft
- Optimizing equipment utilization across your operation
- Streamlining workflows for greater efficiency
Don’t let downtime disrupt your construction projects. Download the free checklist now to start maximizing your uptime with Geotab.
Subscribe to get industry tips and insights
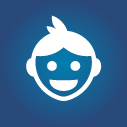
The Geotab Team write about company news.
Table of Contents
Subscribe to get industry tips and insights
Related posts
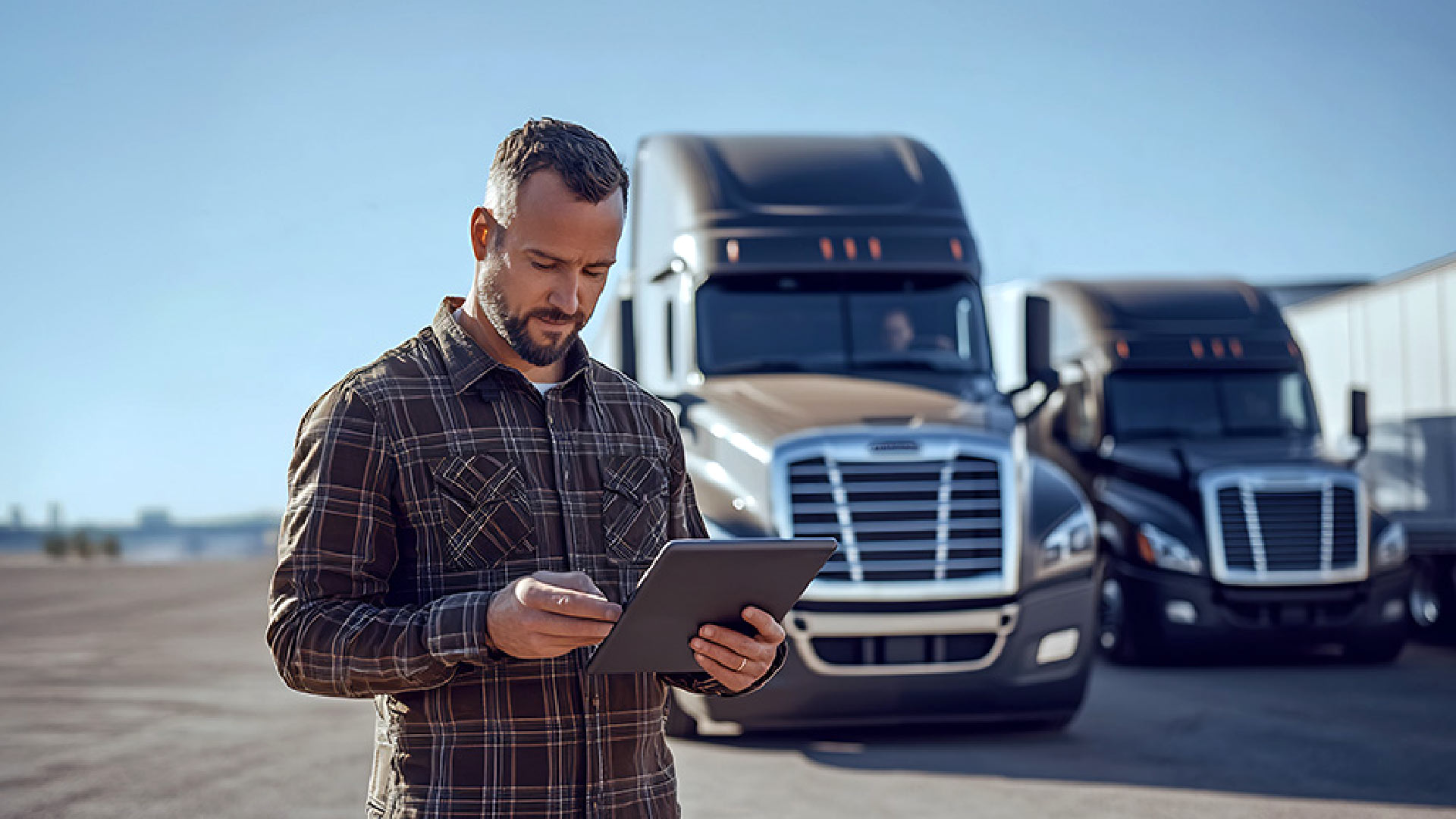
How a well-built fleet safety culture prevents legal trouble
March 28, 2025
5 minute read
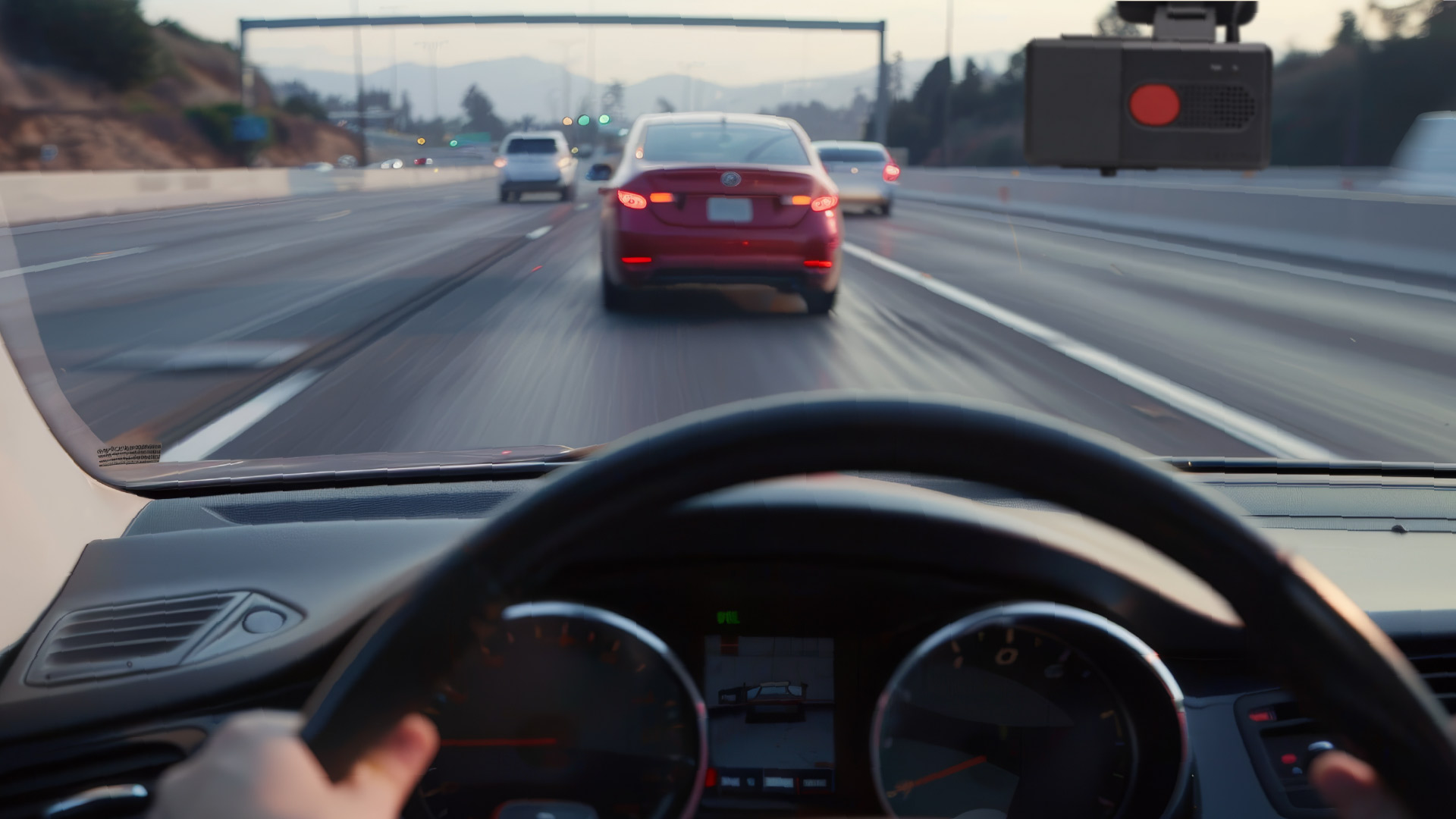
How AI-based in-cab video can lower fleet insurance costs and improve safety
March 24, 2025
3 minute read
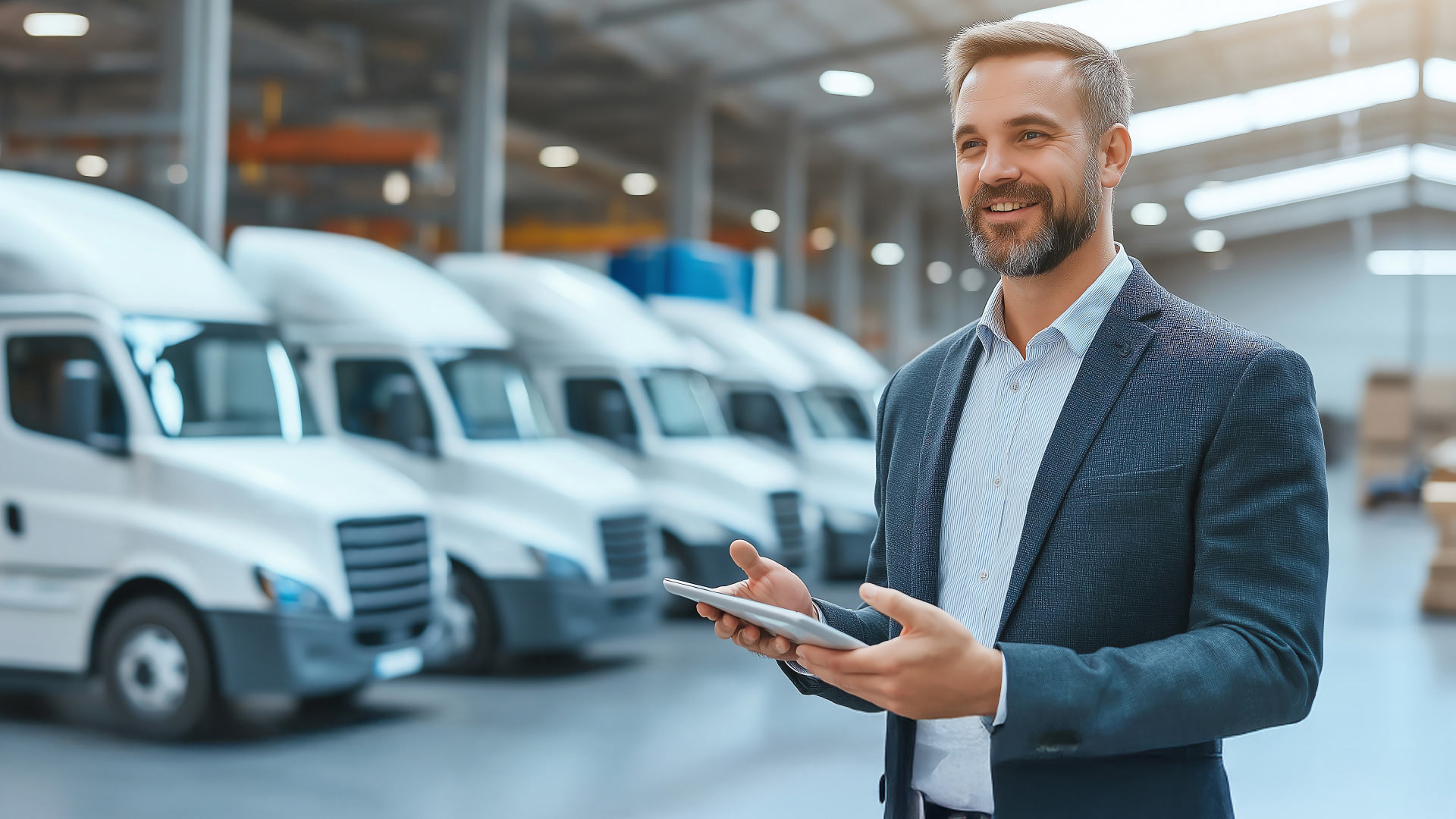
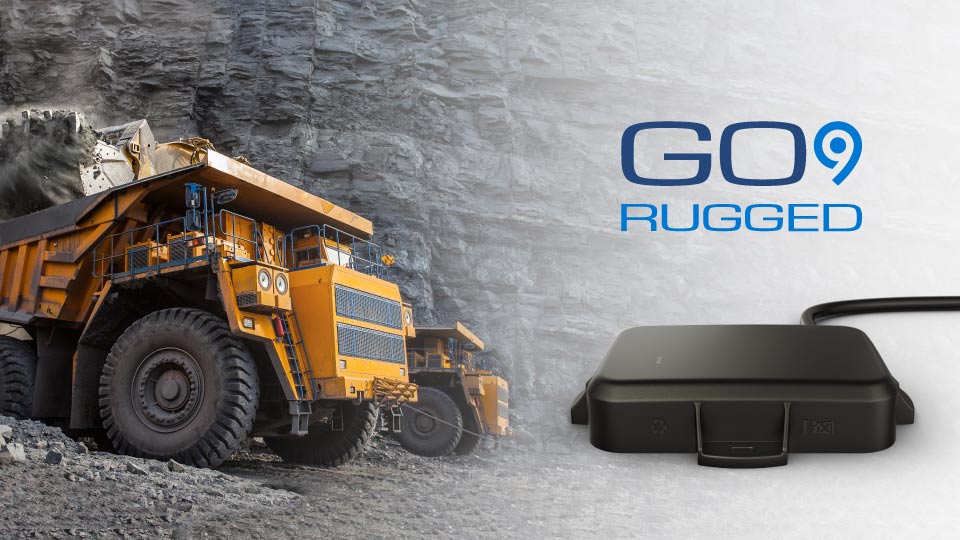
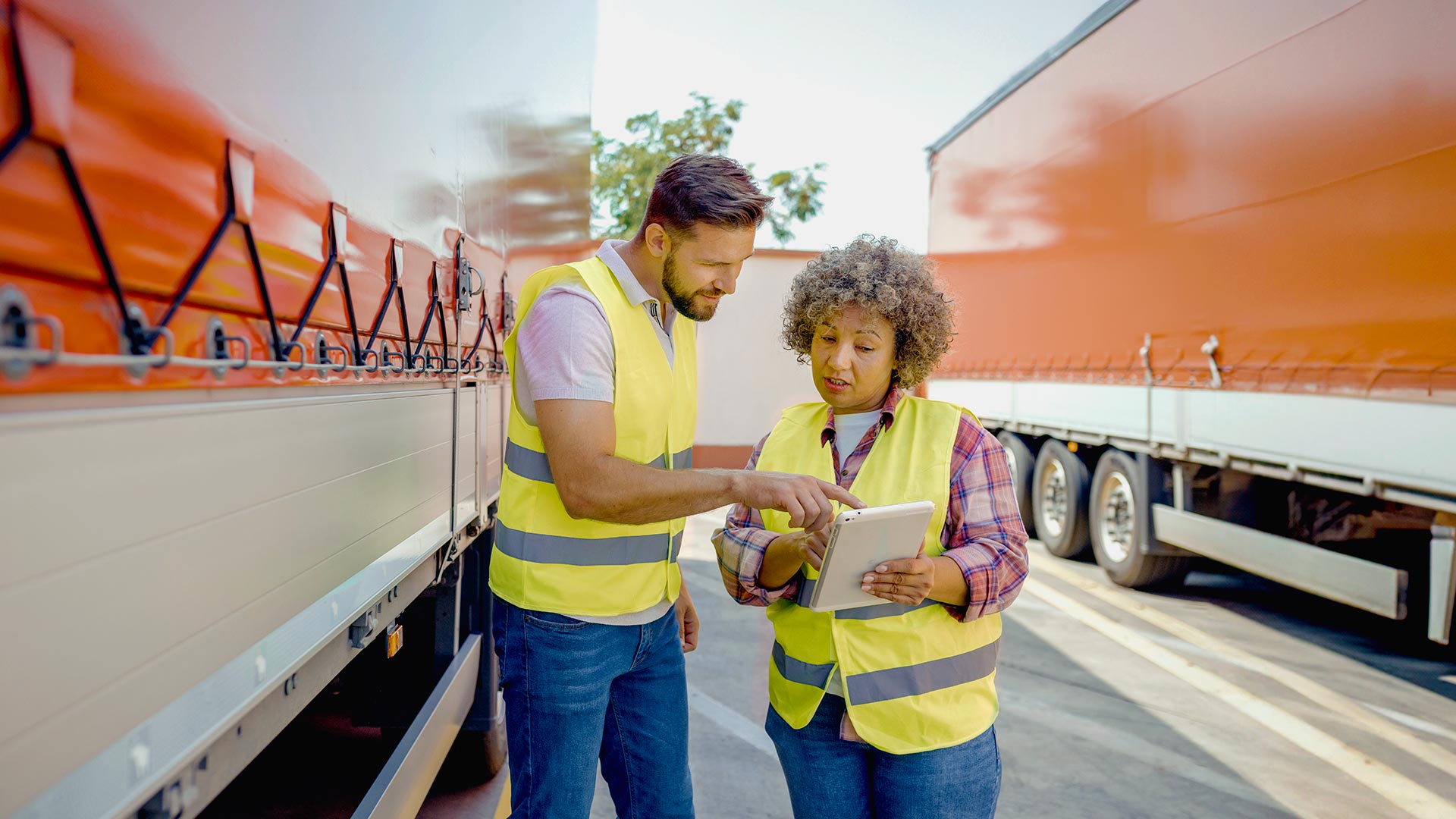
Why driver incentive programs fail and what fleets can do about it
February 27, 2025
5 minute read