4 must-have reports for heavy equipment maintenance managers
Maximize productive uptime with these maintenance reports.
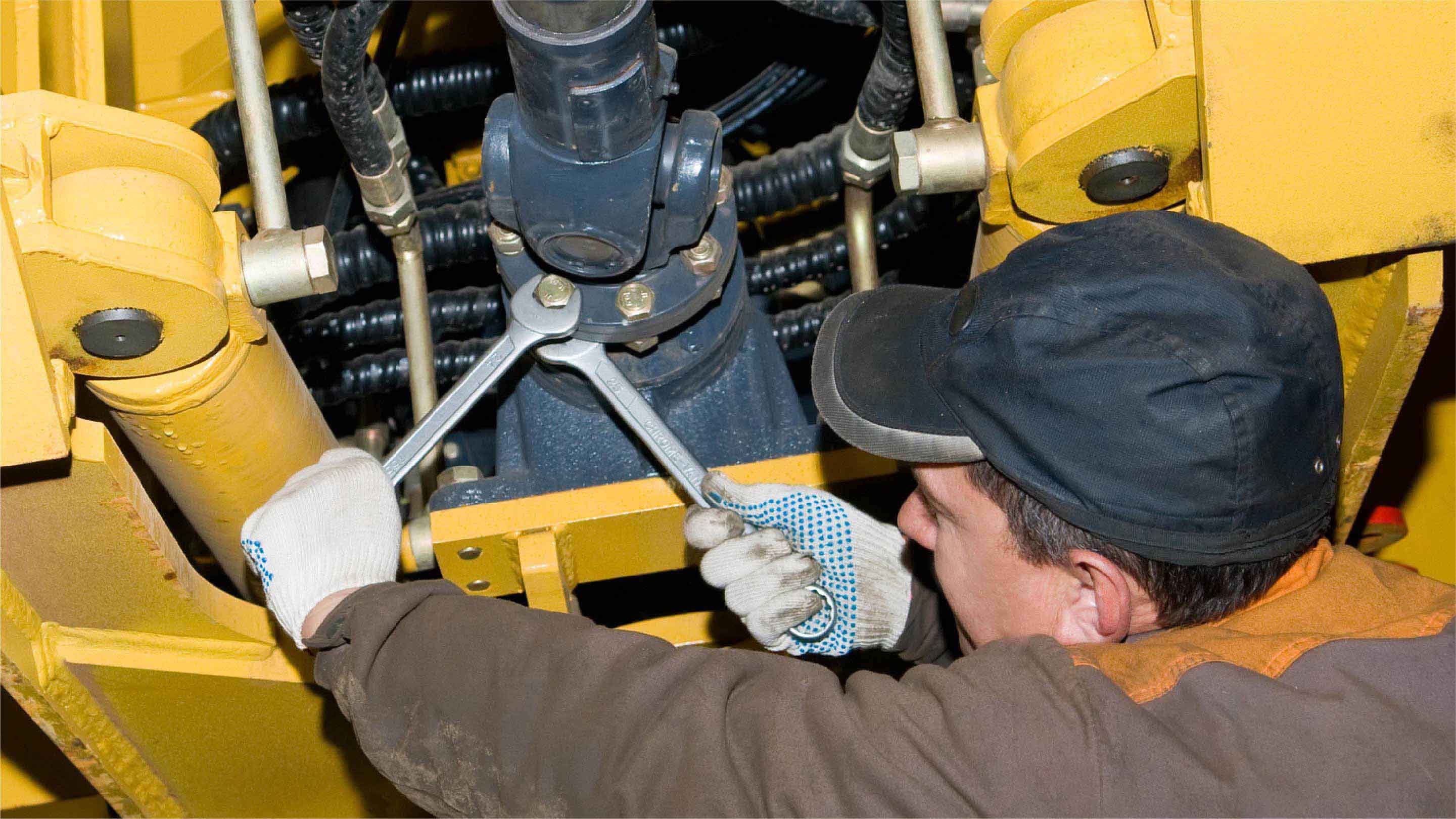
Equipment uptime can be one of the most important factors to consider in your business. Better uptime leads to higher availability, higher utilization and an increase in shift productivity. These mean only good things for both a project’s timeline and its bottom line.
Four fleet reports to help managers meet their uptime requirements
Fault report
The GO device receives fault information from messages read directly from the equipment’s engine computer. These messages, called DTC codes, are translated into an easy-to-understand name in the case of a standard fault and left as its raw DTC code in the case of a proprietary or manufacturer specific fault. These faults can then be pulled and exported using Geotab’s built-in fault report.
Faults can be symptoms of a larger root cause and can be good indicators of impending unplanned downtime. Getting ahead of them gives managers the headstart they need to avoid a potentially costly breakdown.
.png)
Figure 1: An example of a custom Fault Report displaying OBD Fault P-Codes
Maintenance history report and maintenance reminders
MyGeotab has features for storing a history of maintenance records as well as completed maintenance along with the ability to set reminders for planned maintenance based on time, distance travelled or engine run time. A complete record ensures that all vehicles have gone through the check-ups required to keep them running smoothly during a project.
 (1).png)
Figure 2: An example of a maintenance reminder report.
.png)
Figure 3: An example of how your maintenance history report will look.
Engine hours
This is one of the most common methods to track planned maintenance in the construction industry. Engine hours are preferentially pulled directly from the vehicle's engine computers. In the image above, the source of the data are the electronic modules contained within the engine. This allows for accurate engine hours time keeping and it can help plan for downtime when needed.
In the case where a three wire installation is used or engine runtime is not sent over the CAN bus network, Geotab uses a complex algorithm that includes several variables to calculate engine run time to be as accurate as possible.
Rules and exception reports
Geotab has a highly flexible rules engine that can be used with engine data or environmental information. They can be used for the following:
- Environmental data in particular examples
- Dangerous zones can be geofenced for specific vehicle types
- Once rules are broken, they appear in exception reports for anyone to analyse and discuss with employees
- Exception reports can highlight ways to improve fleet operation based on context:
- Vehicles that violate a rule based on these geofences can be inspected for damage
- Drivers that violate rules can be coached towards best practice
- Once vehicles avoid unnecessary areas, maintenance and lost time injury can be avoided
.png)
Figure 4: An exceptions summary report.
Conclusion
To learn more about telematics for heavy equipment transport, download our Quick guide to off-road fleet tracking or visit geotab.com/offroad for more details.
Subscribe for more fleet best practices and tips and tricks.
Subscribe to get industry tips and insights
Rafael Nazareno is a Solutions Engineering Team Lead at Geotab.
Table of Contents
Subscribe to get industry tips and insights
Related posts
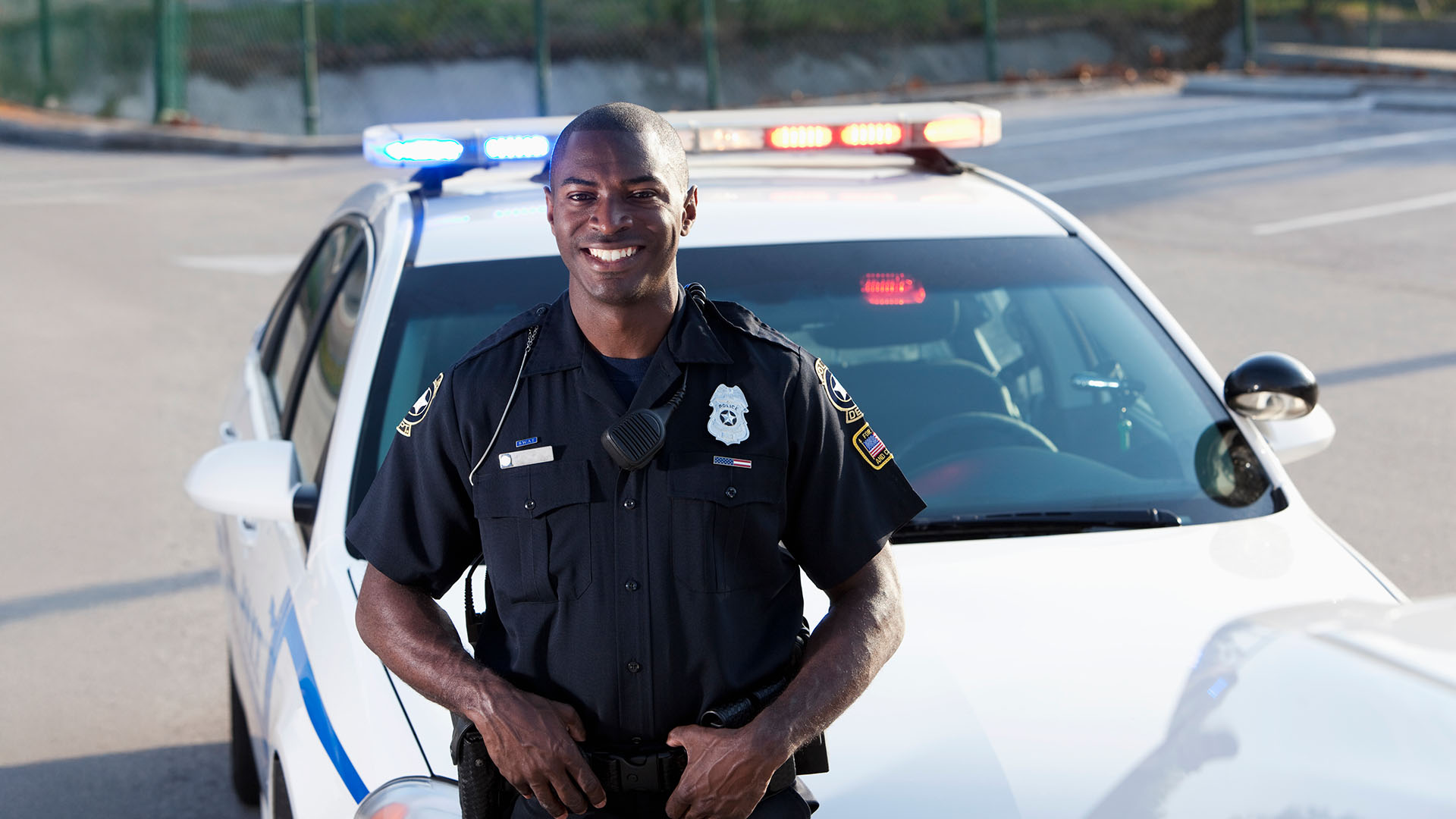
The impact of unproductive idling on police vehicle service life
June 10, 2025
3 minute read
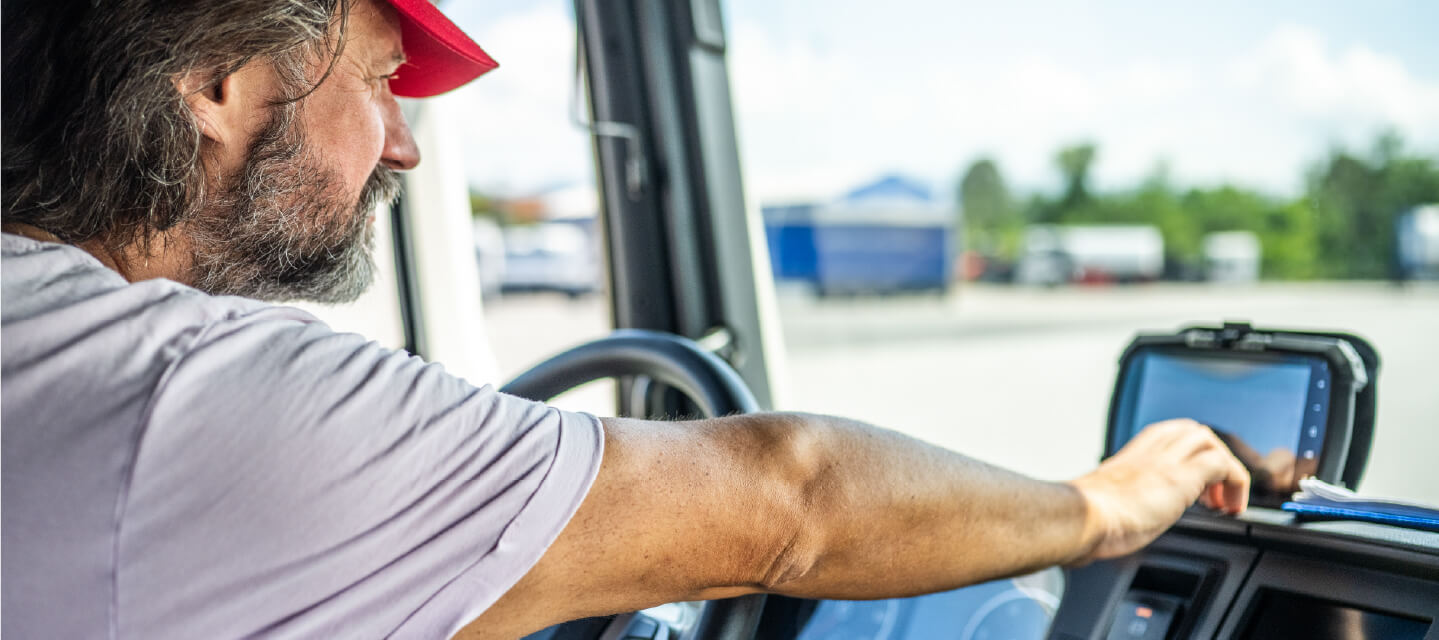
Multi-stop route planners: A fleet manager's guide + best tools in 2025
June 5, 2025
5 minute read
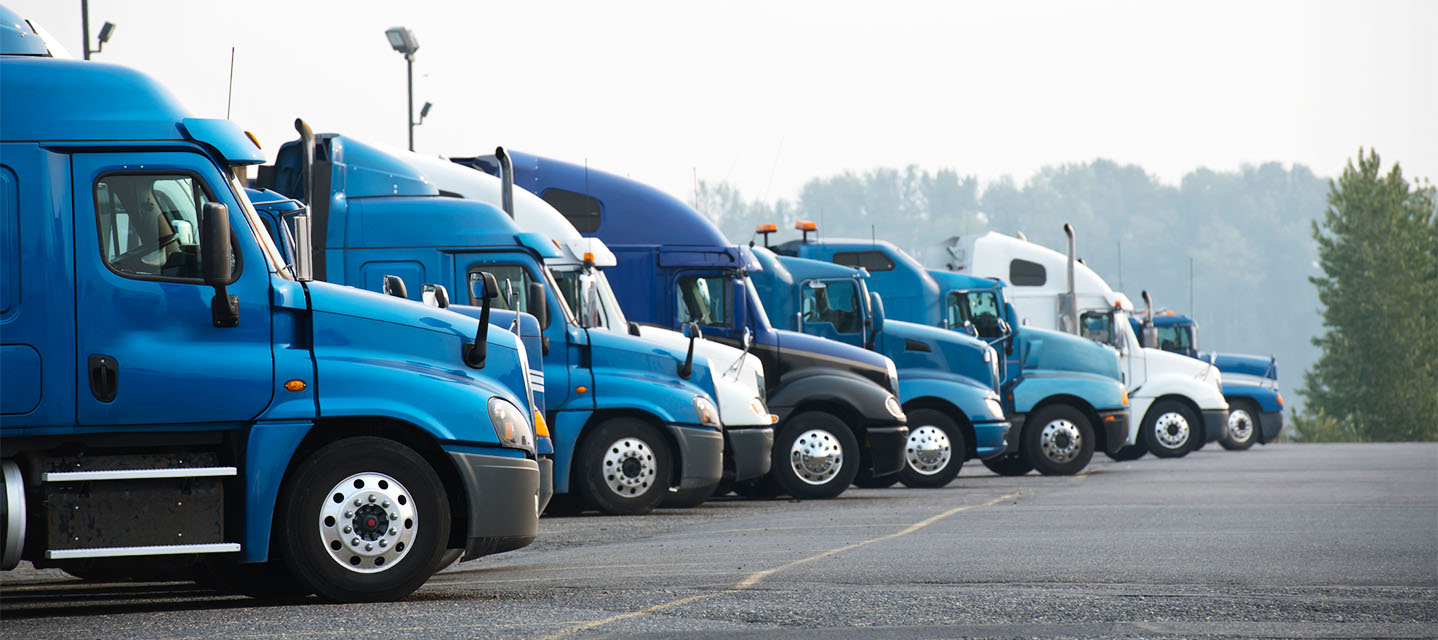
Commercial truck insurance cost: Rates by state + how to save
June 5, 2025
5 minute read

The ROI of telematics for truck lessors: Turn data into profit
May 27, 2025
3 minute read