Telematics and advanced product quality planning
Like other tech industries, demand for newer and better telematics products is constant. Advanced Product Quality Planning (APQP) pushes innovation further.
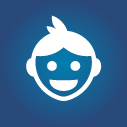
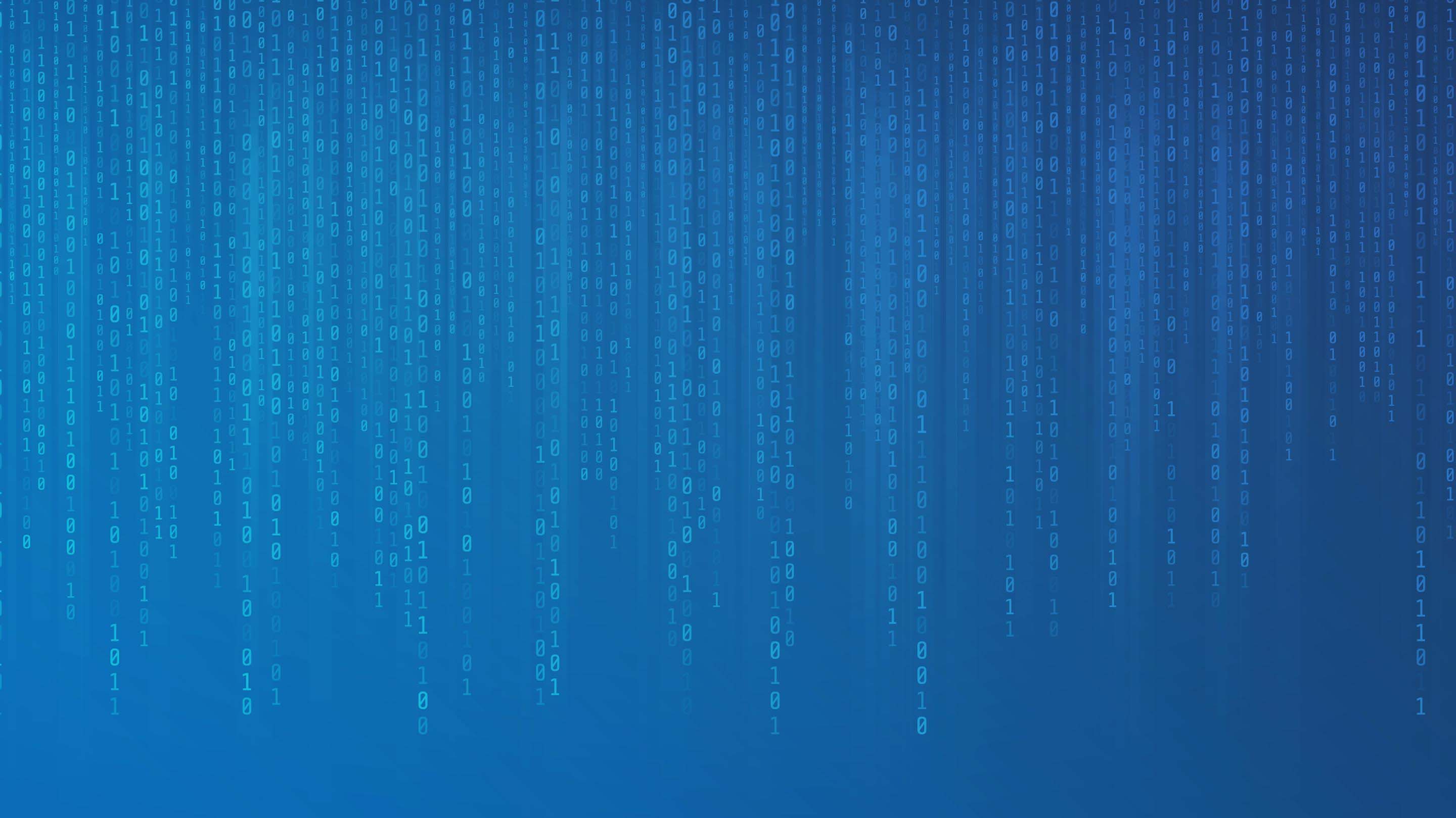
In today’s rapidly changing world, demand for newer, better, and faster telematics products is constant. It is more important than ever to ensure the fundamentals and philosophies of product quality and process design are implemented and maintained.
Advanced Product Quality Planning (APQP) provides us with a sound structure that can be flexible enough to accommodate this innovative industry. APQP is structured to accommodate all the phases from concept to full production of a product to ensure the customers’ needs are met while providing a detailed path of progression. Below are some core concepts of APQP.
Plan and Define:
Having a clear goal in mind, defining concepts, strategies and voicing the customer are crucial to maintaining timelines. It is essential project planning to make necessary adjustments for potential delays that can impact tight deadlines in the future. Outputs of this phase should include:
- Design and quality goals
- Preliminary B.O.M.
- Process flows
- Listing of special characteristics
- Management support
Product Design and Development:
This phase is designed to ensure a comprehensive and critical review of engineering requirements that assess potential problems that could occur during manufacturing. This section ensures all the departments are on the same page and working towards a well-designed product that is capable of being manufactured at the expected costs. Outputs of this phase include:
- Design Failure Modes and Effects Analysis
- Design for Manufacturability
- Design Reviews
- Engineering Drawings
- Material Specifications
Process Design and Development:
Towards the end of the design and development phase, this section begins and encompasses development of an effective manufacturing system. Planning how the product will be assembled and packaged in its final form. The manufacturing system assures that the customer requirements and expectations will be met with the final product. Some outputs from this phase should include:
- Process Flow Chart
- Product / Process quality system review
- Process Failure Modes
- Effects Analysis
- Process Instructions
Product and Process Validation:
At this stage the product is set for production and there should be a validation of the product after it has been run through the expected process. This vital stage ensures there are no anomalies associated with the process and that the product meets the intended design goals and customer’s needs. Outputs of this stage include:
- Preliminary Process Capability
- Production Validation Testing
- Production Control Plan
- Quality Planning Sign-off
Feedback, Assessment and Corrective Action:
Quality planning does not end with process validation, there must still be an open channel for feedback to reduce variation in the process and correct the shortcomings. This is also a stage to assess the overall effectiveness of the product quality planning effort. Outputs of this stage are: Reduce variation, Customer satisfaction and Delivery and Service. This stage can also lead to product improvements and next generation models based on the outputs and so the process would begin again from the Plan and Define Phase.
Integration of all the phases is important to secure a sound design with outcomes that meet the needs of the customer and provide reliable data to reduce risk from engineering and process related issues. Managing the fast changing landscapes with the expected milestones becomes difficult but increasingly important to exceed expectations in the industry.
Contact us to learn more about Geotab’s product quality planning process.
See also: Setting the standard in data quality
Subscribe to get industry tips and insights
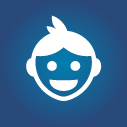
Geotab team
Table of Contents
Subscribe to get industry tips and insights
Related posts
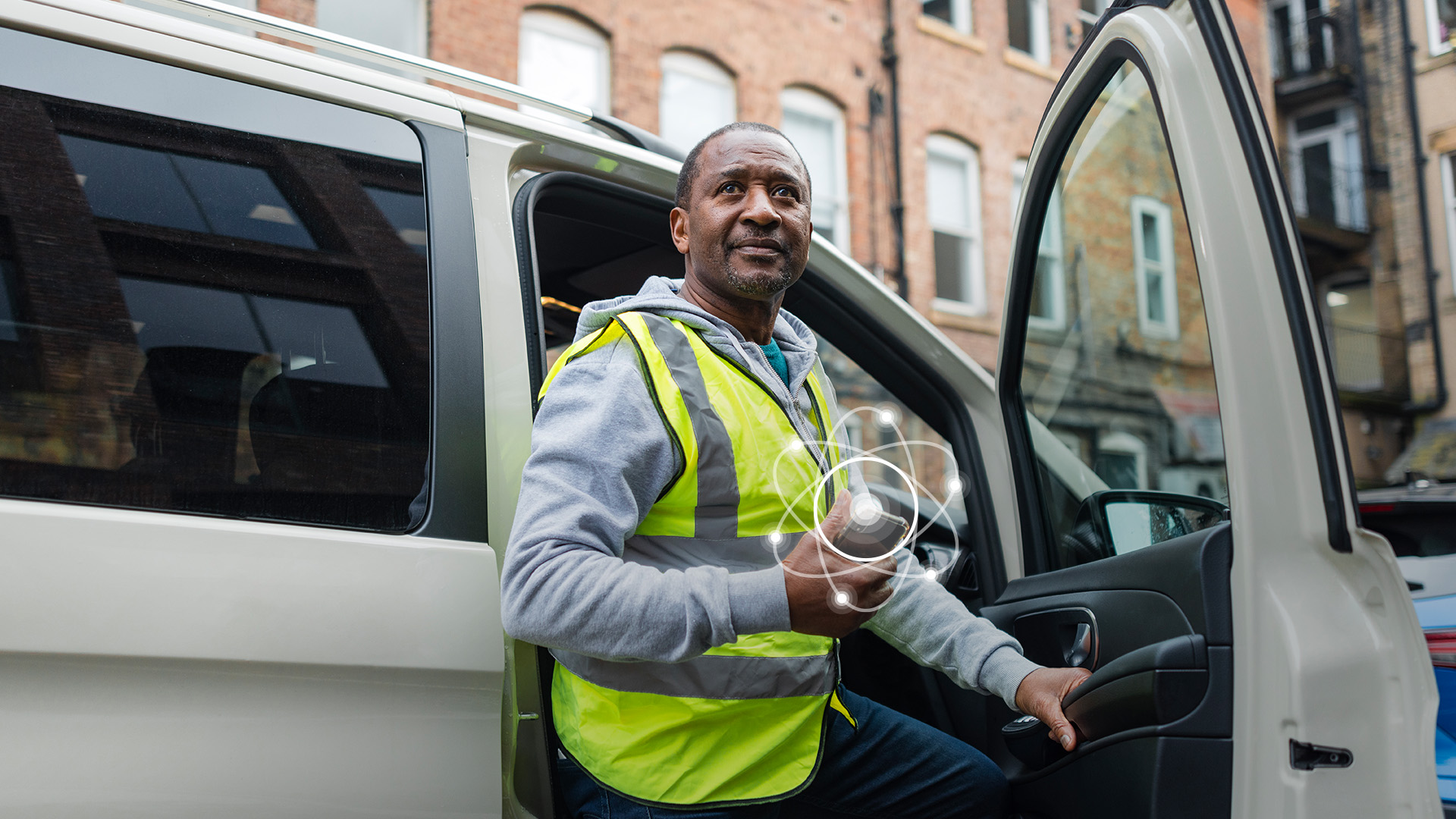
Field service is losing money to bad data: Go beyond GPS with smarter telematics
June 27, 2025
3 minute read
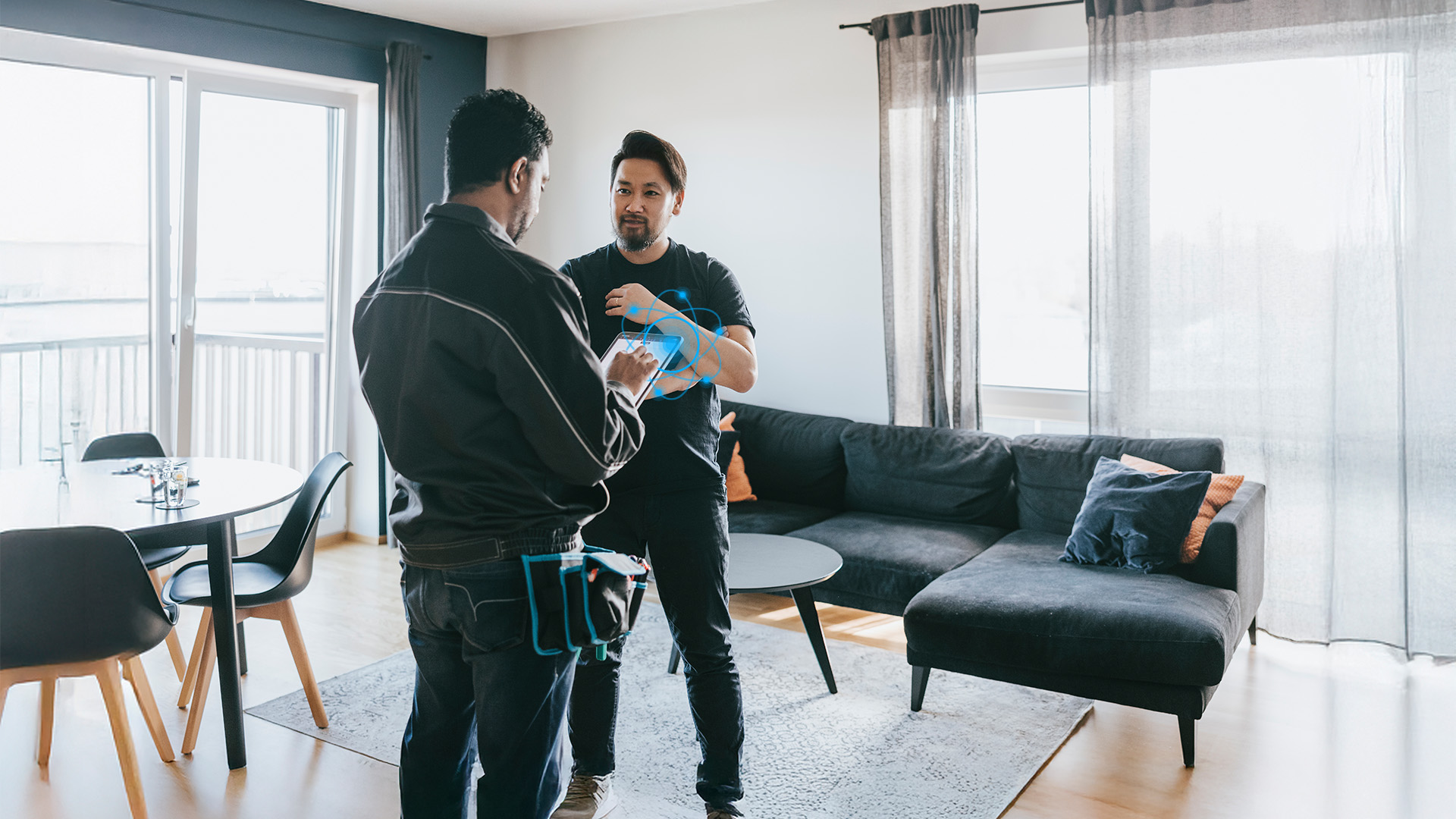
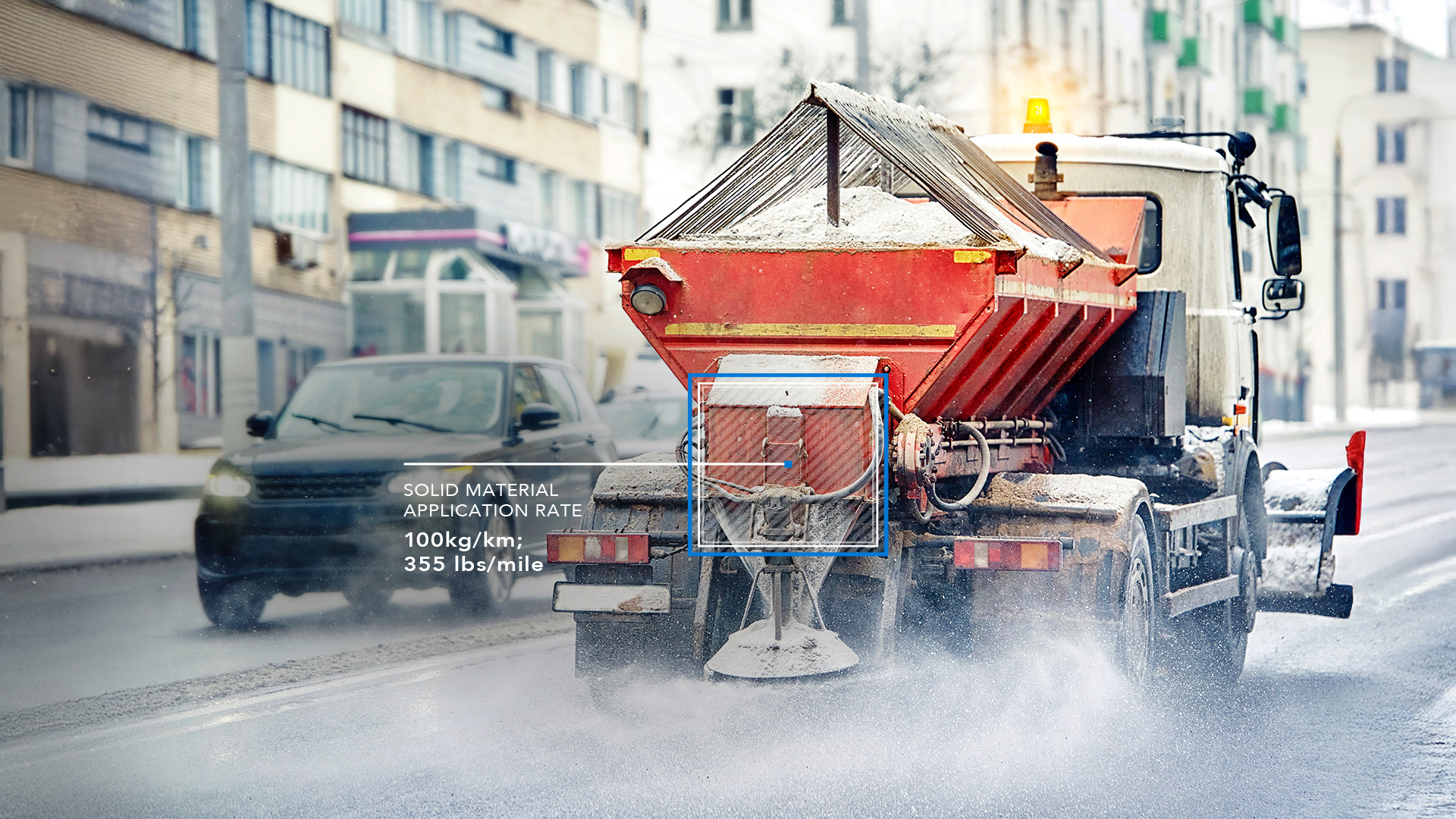
Enhancing winter road maintenance with postseason materials usage analyses
June 20, 2025
6 minute read
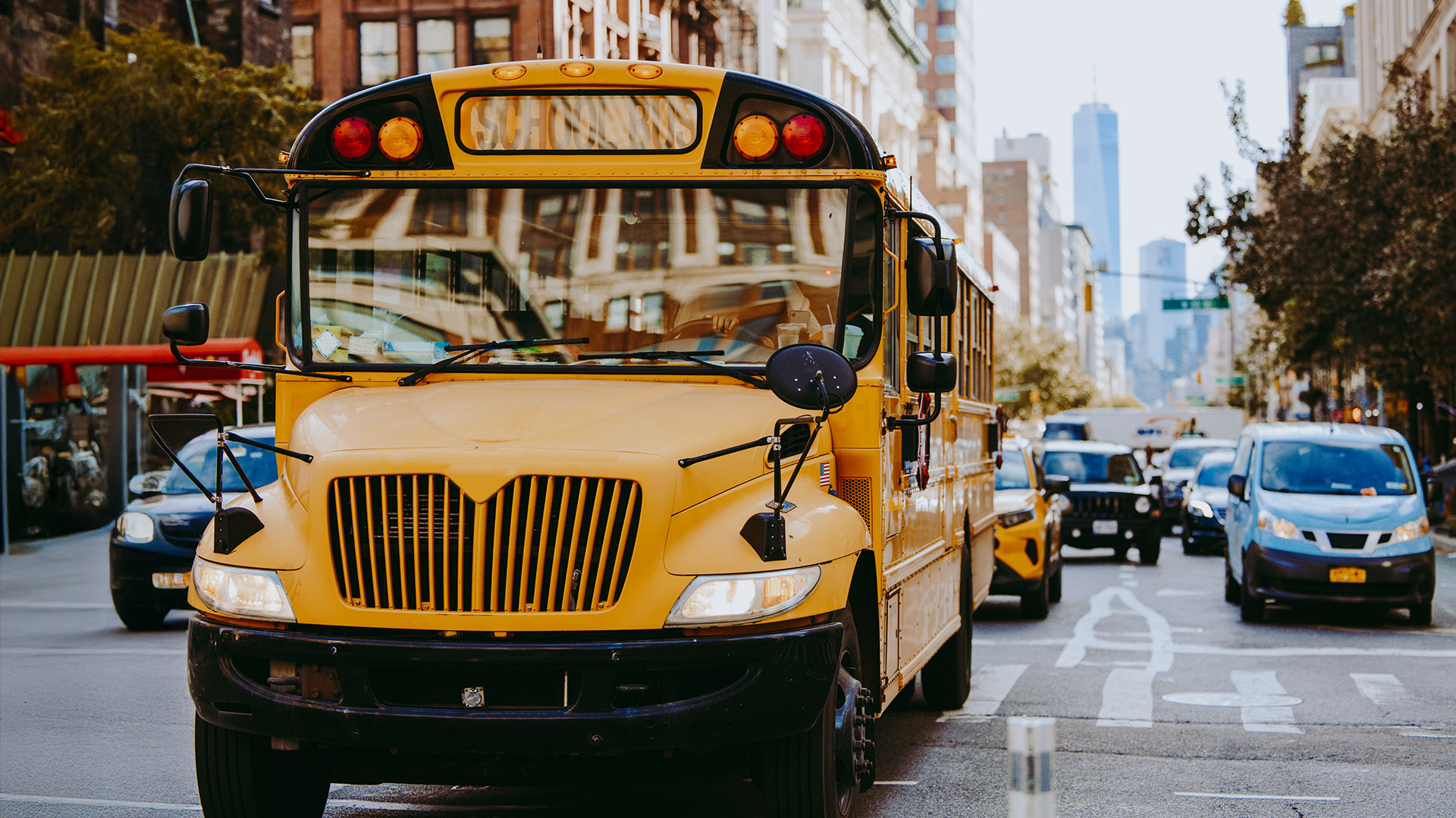
Building a self-sustaining school bus driver safety program with Geotab Vitality
June 13, 2025
7 minute read
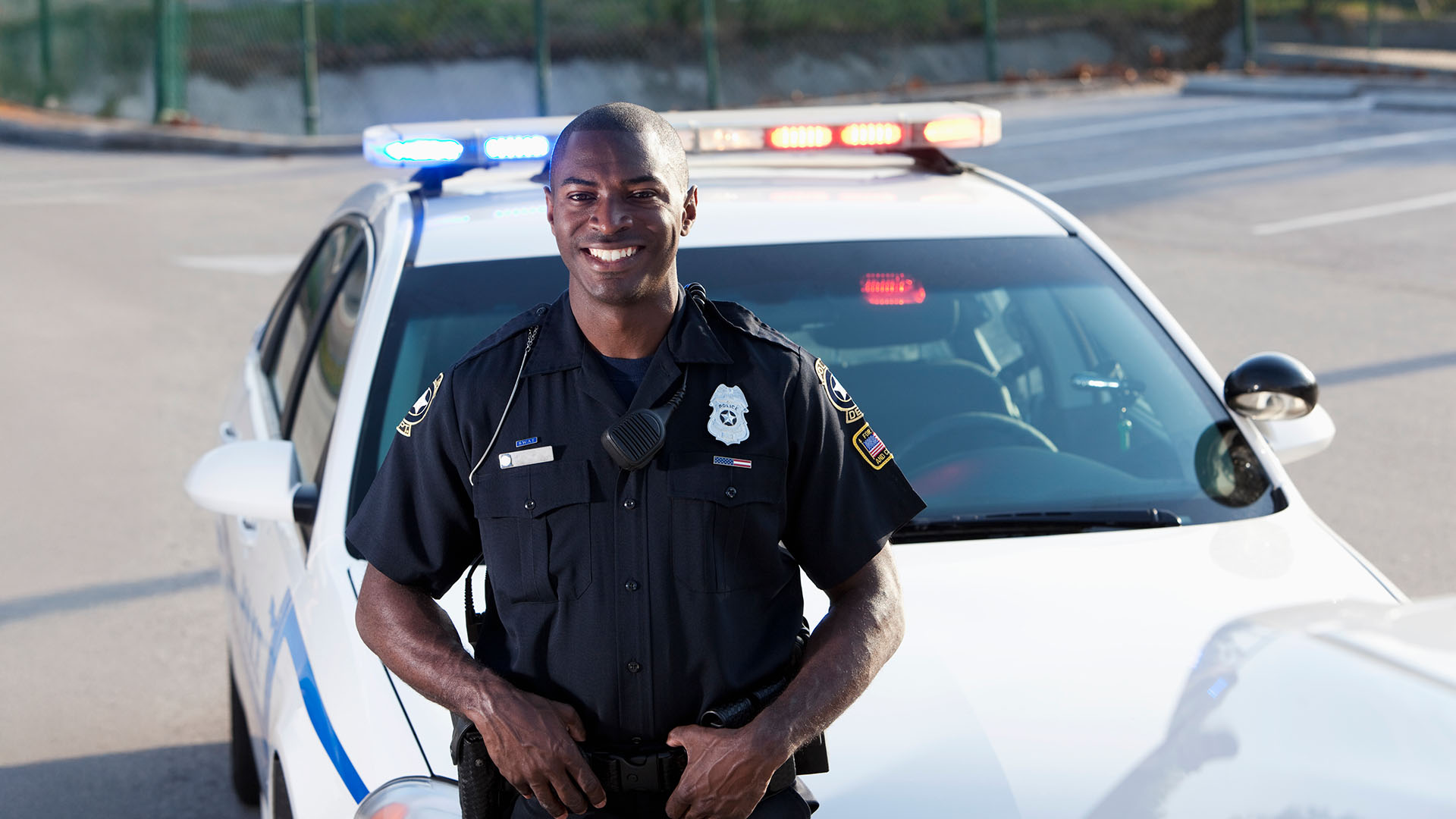
The impact of unproductive idling on police vehicle service life
June 10, 2025
3 minute read
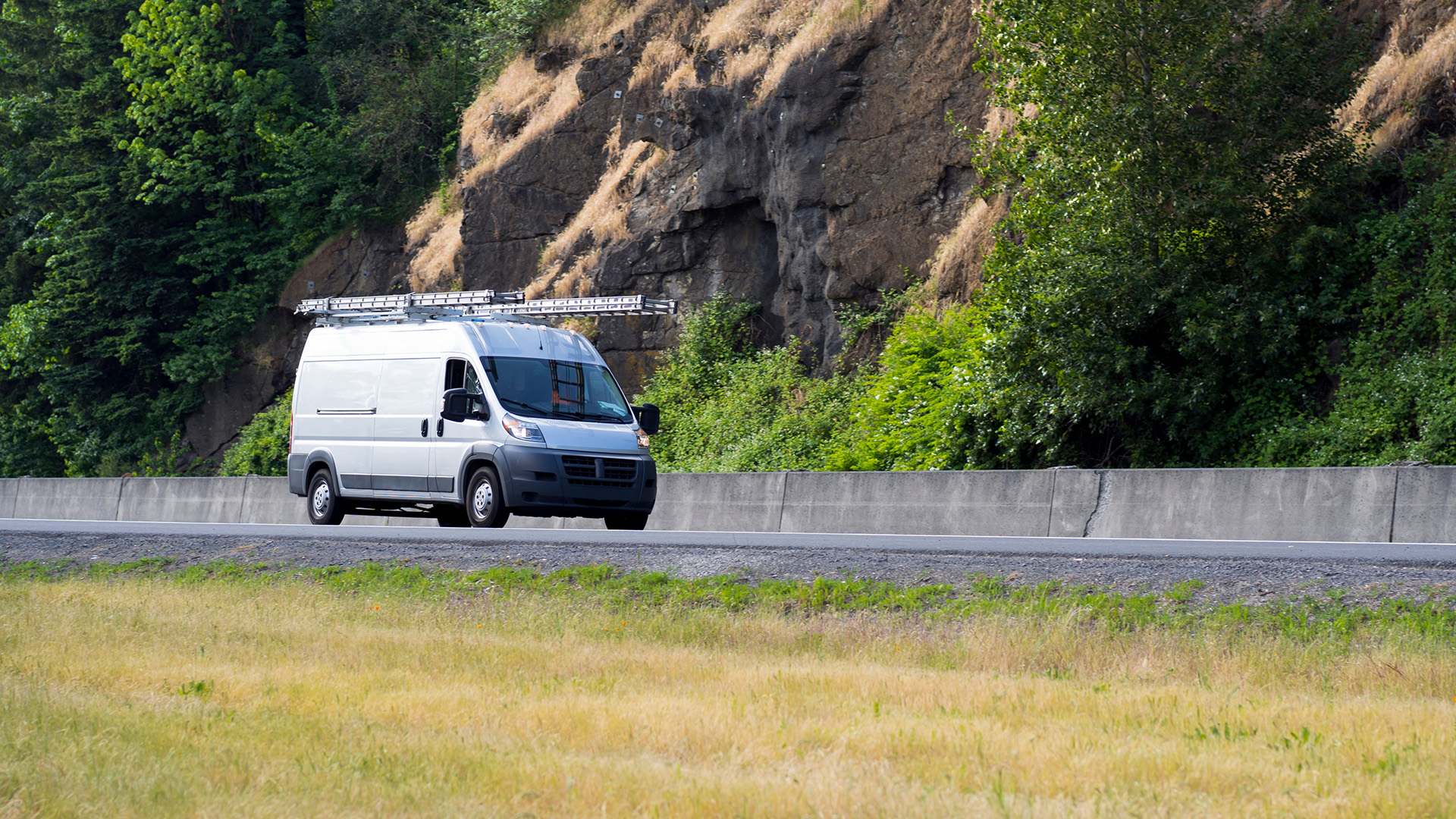
Unlock field service ROI: Your practical guide to connected operations playbook
June 9, 2025
3 minute read