What is an air-ride suspension? The pros and cons
March 13, 2025
•2 minute read
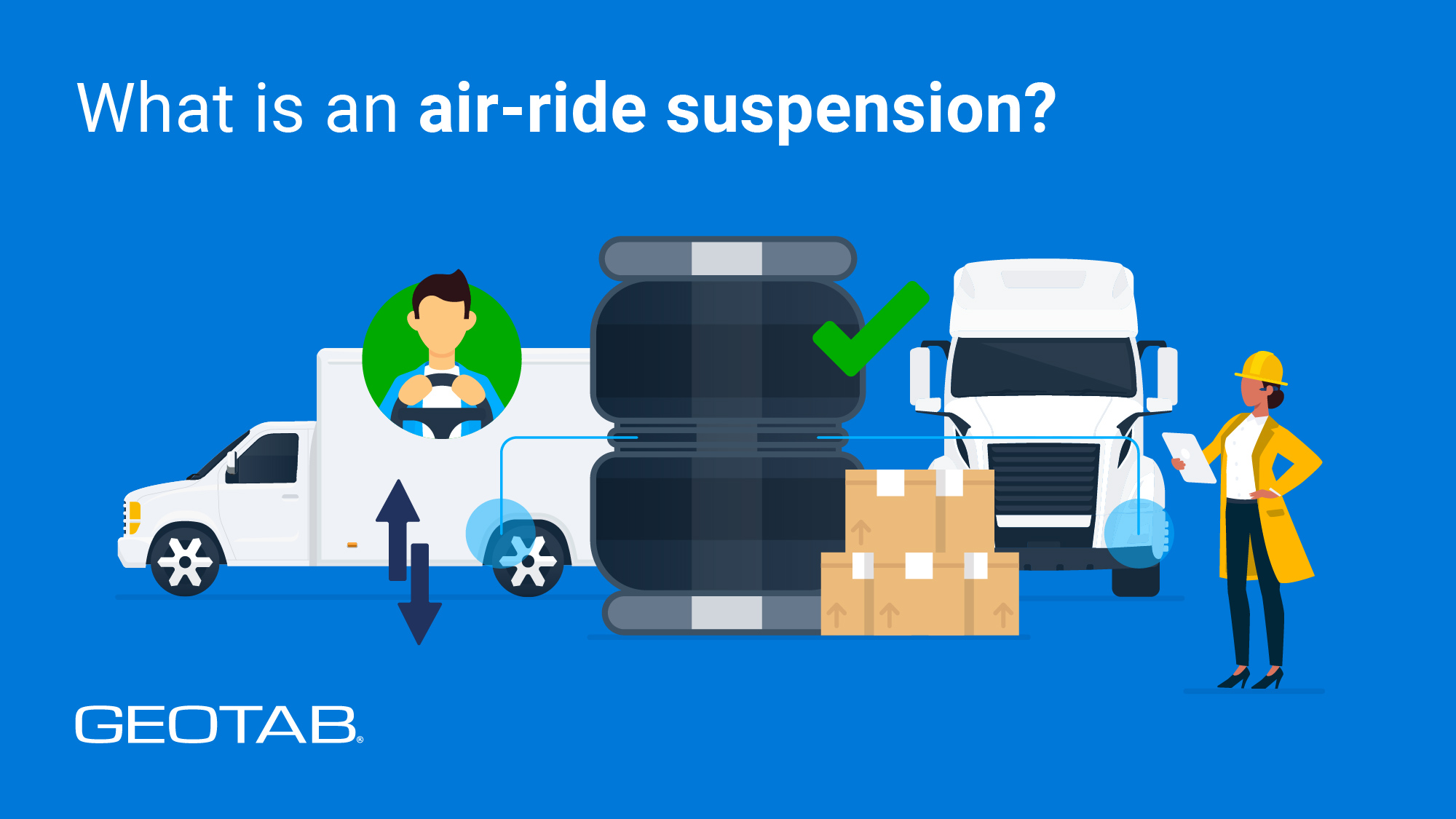
Key Insights
- Air-ride suspension is a type of vehicle suspension system that replaces traditional steel springs with air-filled rubber bellows, which are also known as air springs.
What is an air-ride suspension?
Air-ride suspension is a type of vehicle suspension system that replaces traditional steel springs with air-filled rubber bellows, which are also known as air springs. This suspension system uses compressed air to adjust the vehicle’s ride height and absorb road shocks, giving drivers a smoother and more controlled ride. Fleet managers often rely on air-ride suspension to improve driver comfort, protect cargo, and extend the lifespan of commercial vehicles.
In this glossary blog post, we will examine how air-ride suspensions work, the pros and cons of an air-ride suspension, and how fleets can best use air-ride suspensions in transportation.
How does an air-ride suspension work?
An air-ride suspension system operates through a network of air springs, compressors and control systems that maintain optimal vehicle height and ride quality. Here’s a step-by-step description of how the key components of air-ride suspensions work:
- Air springs: These flexible rubber bellows inflate with compressed air to support the vehicle’s weight and absorb road vibrations.
- Air compressor: This pressurizes air and sends it to the air springs, distributing the compressed air wherever it’s needed to support the vehicle as it moves or changes its load.
- Sensors and valves: Height-control sensors regularly detect small changes in the vehicle’s load or the terrain, then send signals to the system’s valves to adjust air pressure accordingly.
- Control system: Drivers or automated systems can adjust the air-ride suspension’s height and sensitivity to maintain optimal ride comfort and stability.
Air-ride suspensions continuously adapt to road conditions, vehicle load, and driver preferences, improving the driver experience and reducing wear on a vehicle’s frame and components.
Air-ride suspension vs leaf spring suspension
The primary difference between air-ride suspension and leaf spring suspension is the way they absorb shocks and distribute vehicle weight.
Air-ride suspensions use air springs instead of metal springs, giving drivers a smoother ride by adjusting air pressure based on load weight and road conditions. This also reduces vibration and stress on cargo, making air-ride suspensions great for fragile loads. Air-ride suspensions are most common in long-haul trucks, luxury vehicles and specialized fleet applications.
Leaf spring suspensions rely on stacked layers of curved metal strips known as leaf springs to absorb shocks as a vehicle moves. These provide better load-carrying capacity but tend to cause a stiffer and less comfortable ride. Leaf spring suspensions are common in heavy-duty trucks, trailers and off-road vehicles.
For fleets, leaf spring suspensions are generally more durable and cost-effective, while air-ride suspensions provide superior ride quality and cargo protection.
Pros and cons of air-ride suspension
Pros of air-ride suspension:
- Enhanced ride comfort: Reduces driver fatigue by minimizing road shocks and other effects from stiffer suspension.
- Cargo protection: Delivers a smoother ride that helps prevent damage to fragile freight.
- Better vehicle stability: Maintains consistent ride height and weight distribution for easier operation across load and road conditions.
- Improved life of assets: Lessens wear and tear on vehicle components and trailers, helping them last longer.
Cons of air-ride suspension:
- Higher initial cost: More expensive to install and repair than traditional leaf spring suspension systems.
- Increased maintenance needs: Requires regular inspection of air components to avoid rust, leakage, moisture damage or compressor burnout.
- Fuel consumption: Uses fuel to run the air compressor, and the heavier weight of air-ride suspensions can make a vehicle consume more fuel.
Application of air-ride suspension
Air-ride suspension is widely used in many sectors of the transportation industry, but most common for over-the-road vehicles. The most common applications of air-ride suspension include:
- Heavy-duty trailers: Air-ride suspensions in flatbeds, refrigerated trailers and tankers help prevent cargo damage.
- Commercial motor vehicles (CMVs): Air-ride suspensions improve ride quality for long-haul trucking operations, helping to reduce driver fatigue.
- Recreational vehicles (RVs): Air-ride suspensions provide a smoother ride and more pleasant travel for motorhomes and luxury buses.
Frequently Asked Questions
The cost of installing air-ride suspensions varies depending on vehicle type and system complexity. A full retrofit for a truck or trailer can range from $3,000 to $10,000.
While air-ride systems require more maintenance than leaf springs, fleet managers can perform routine inspections and proactive maintenance to avoid major issues. Key maintenance tasks include checking air springs for leaks, checking proper compressor function and monitoring control systems.
With proper maintenance, an air-ride suspension system can last 8–10 years. However, individual components such as air springs and compressors will likely require replacement sooner, depending on usage and road conditions.
Other Stories
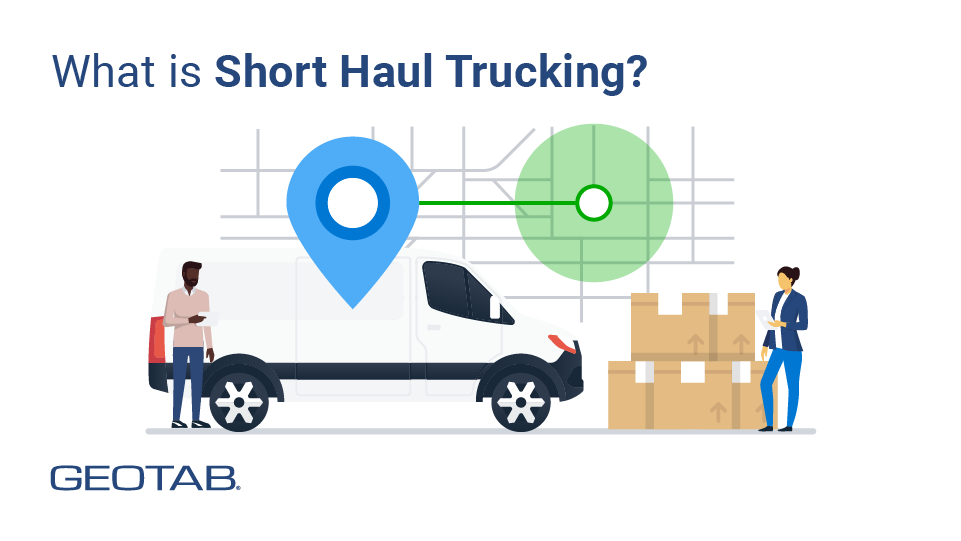
March 20, 2025
4 minute read
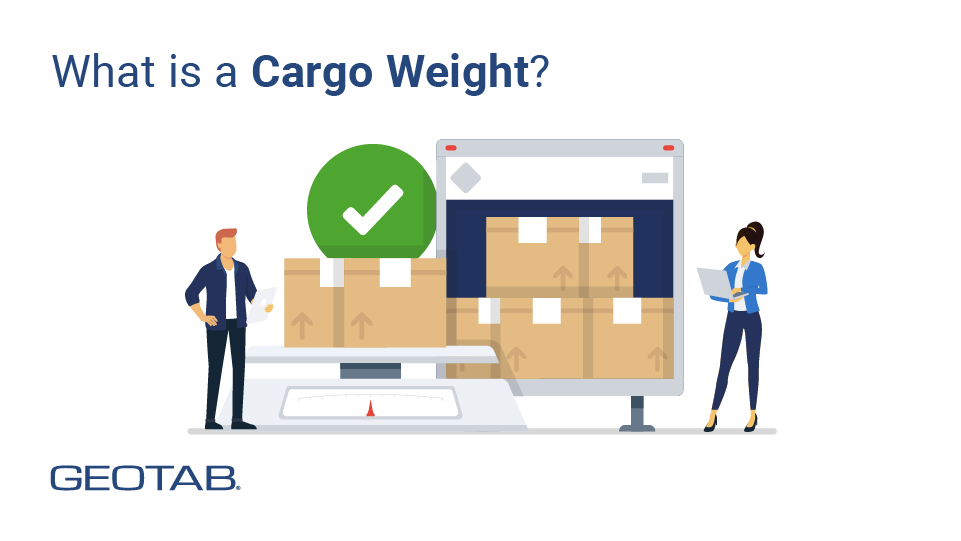
March 20, 2025
3 minute read
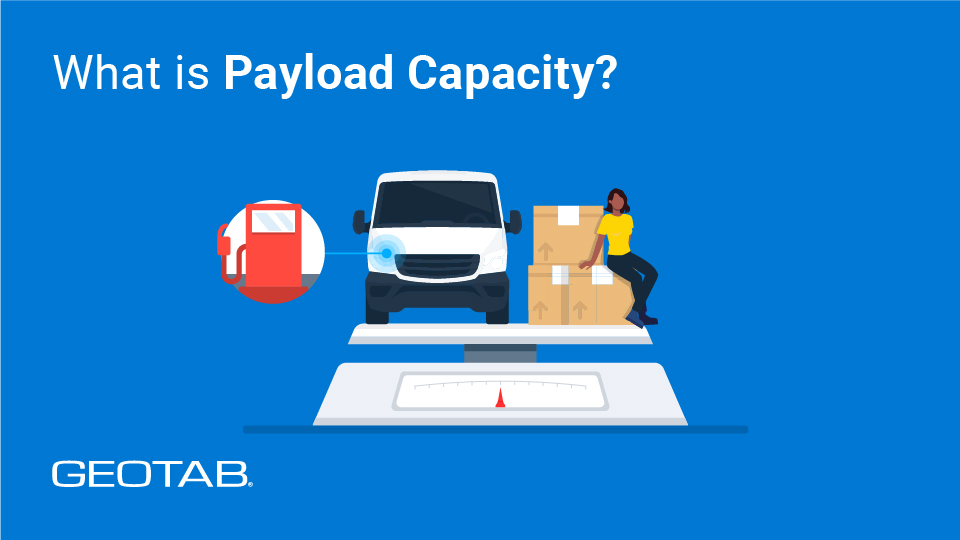
January 29, 2025
4 minute read